Chinese New Year, the grandest festival in China, arrives soon on Jan, 25th, with a 7-day long holiday. And most of the mobile phone charger manufactured factories have up to 30 days (1 month) off work. Most of the suppliers now refuse to accept orders delivery before the holidays. Why it take such a long time to produce a small charger? What is the complexity? You must be curious about the procedures. Let’s have a look into it.
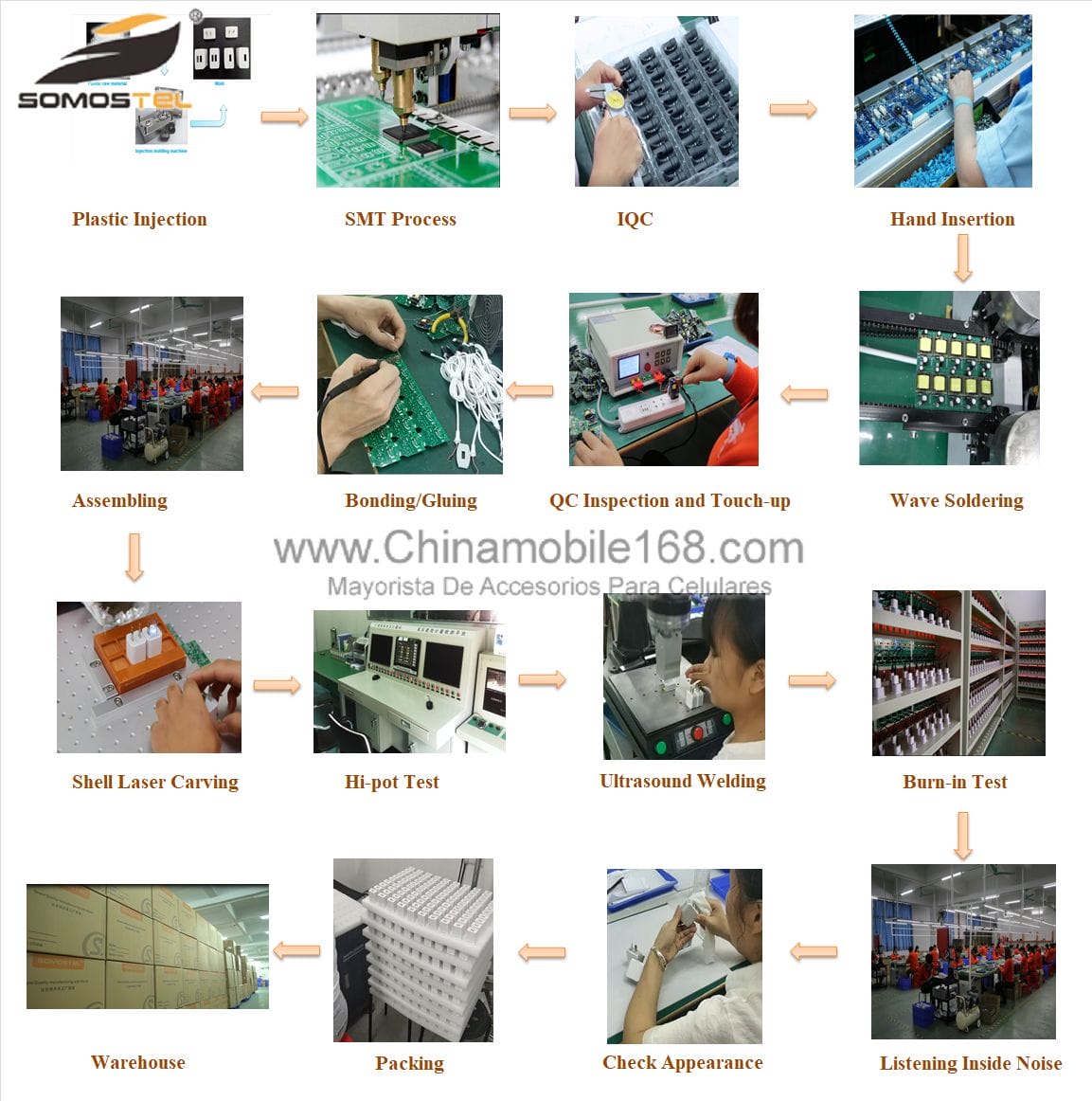
Product Design:
The processes of product design include industrial design (appearance), 3D model print, structural design, electronic design, program confirmation and functional test. To make it brief, it’s a period of sample confirmation before mass production.
Plastic Injection:
The injection molding process requires the use of an injection molding machine, raw plastic material, and a mold. It’s the process of melting raw material into required shape (the charger shell). The plastic is melted in the injection molding machine and then injected into the mold, where it cools and solidifies into the final part.
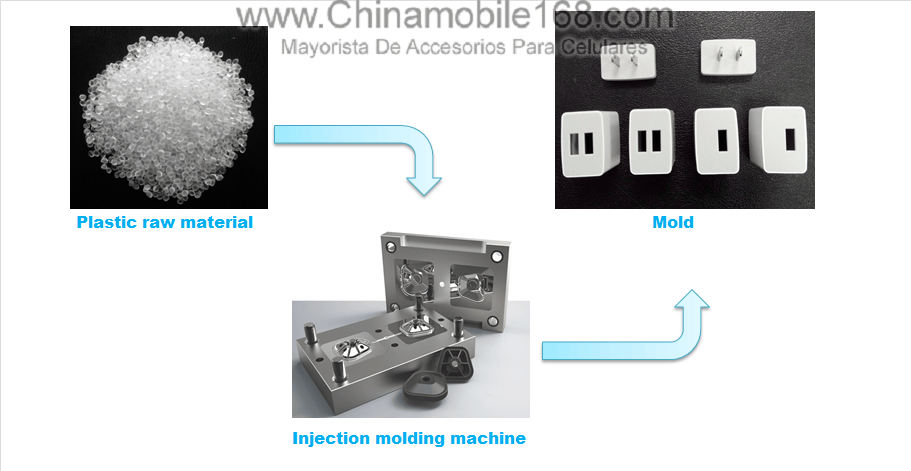
SMT Process:
SMT (Surface Mount Technology) process is to mount electronic components on the surface of suitable substrate. In general terms, it’s a kind of process to manufacture PCBA.
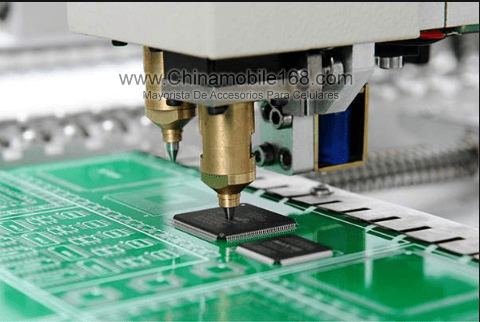
IQC (Incoming Quality Control):
Preparing and checking the incoming assemble materials, including shells, PCB and other components.
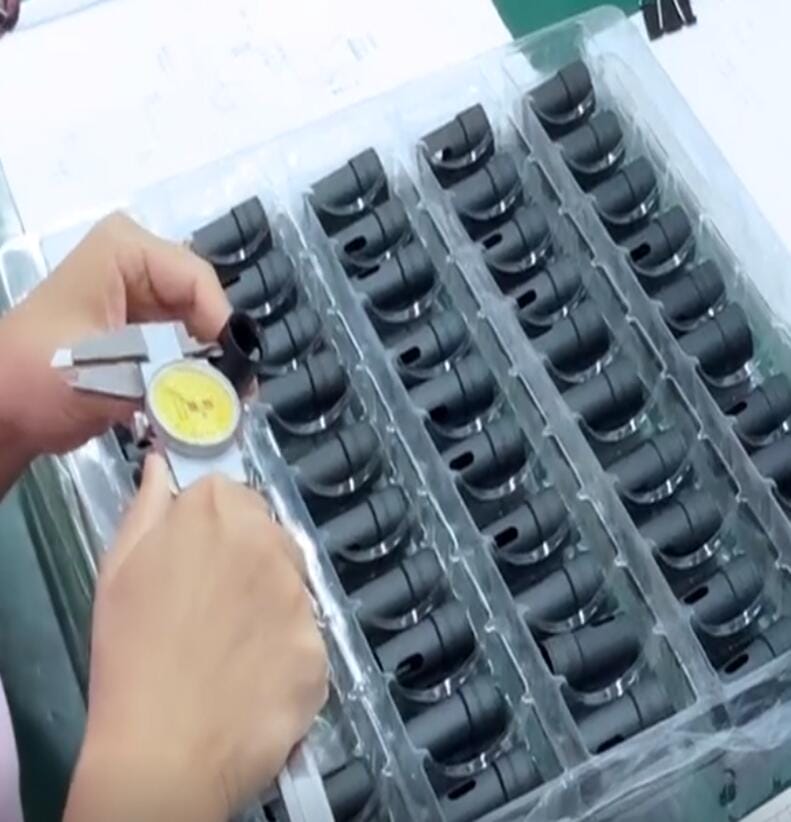
Hand Insertion:
Some oversized electronic components that can’t be mounted to the PCB during SMT process will be inserted to the substrate manually waiting for soldering.

Wave-soldering:
It is a reliable way to get the circuits and components to stick to the board and stay there firmly. The machine creates a “wave” of solder that washes over the board, soldering the components to the board. The PCB then receives a water spray or air blowing to safely cool it and fix the parts in place.
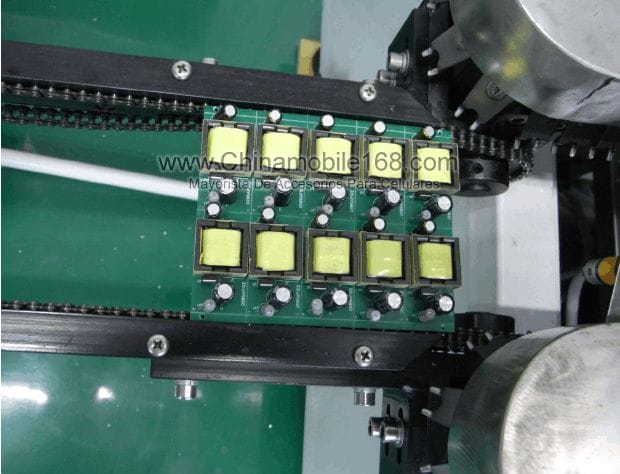
QC Inspect and Touch-up:
After the above processes, all PCB goes to QC, QC inspects and marks all that needs rework then PCB’s goes to Touch-up to fix what QC marked for rework.
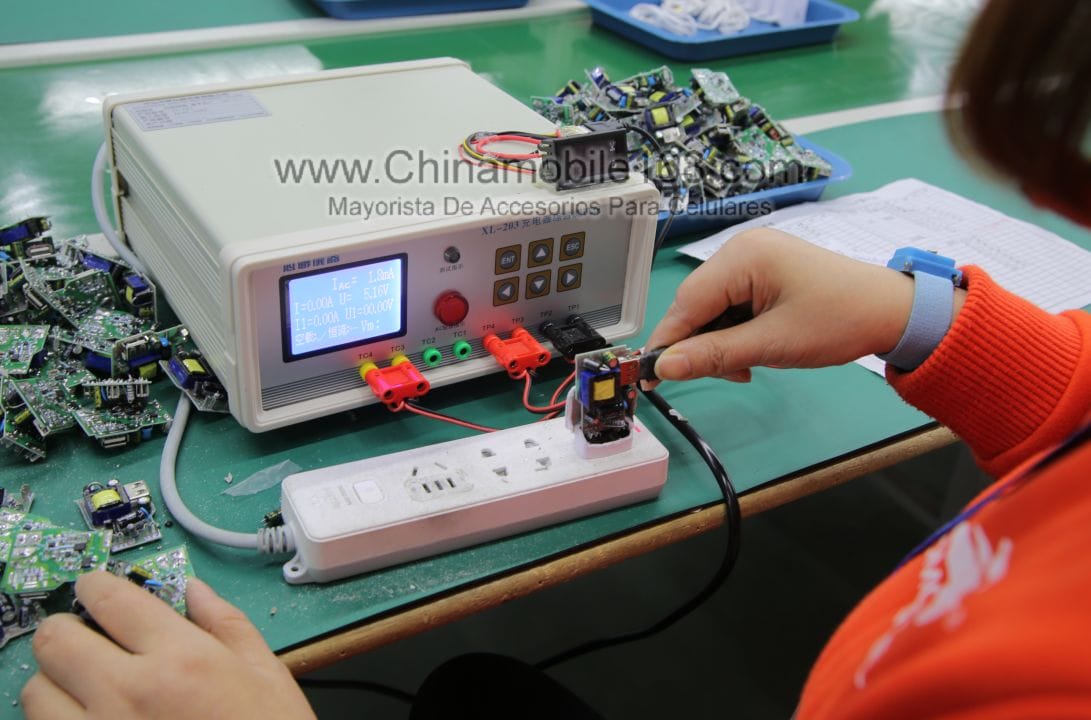
Bonding/Gluing
To solidify the electronic components to the board by adding safety conductive grease.
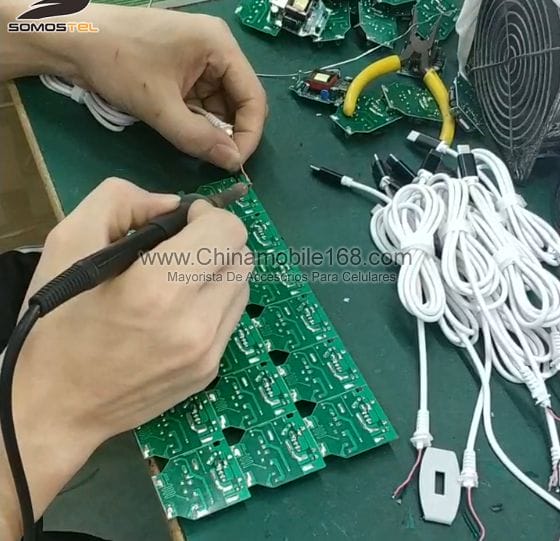
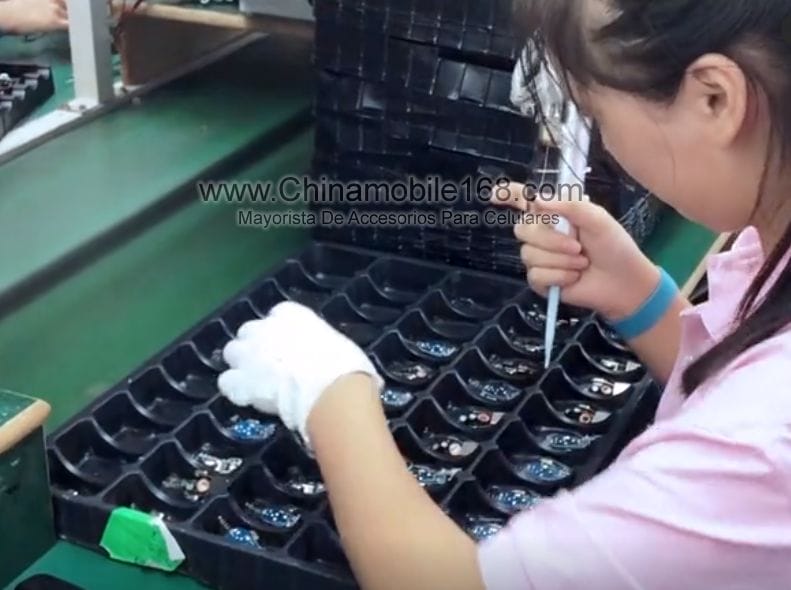
Bonding/Gluing
To solidify the electronic components to the board by adding safety conductive grease.

Shell Laser Carving:
Shell laser engraving, which is a subset of laser marking, is the practice of using lasers to engrave customer logo, specifications or some demanded patterns to the shell.
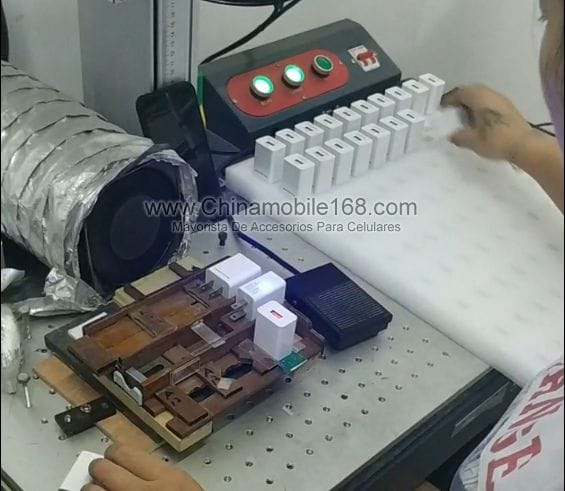
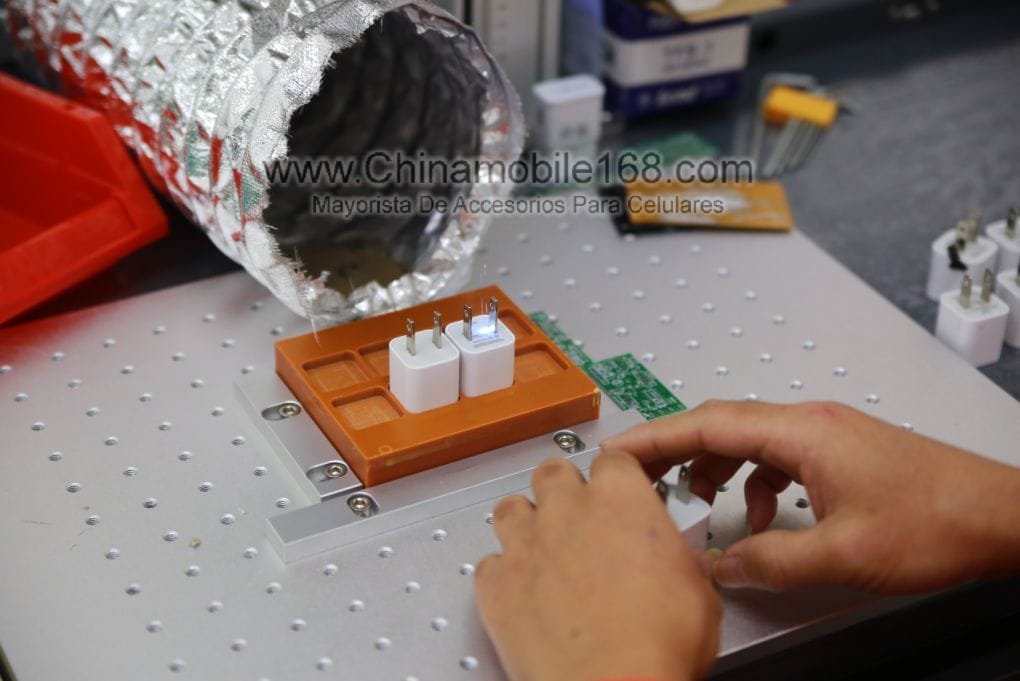
Hi-pot Test
Hi-pot Test is short name of high potential (high voltage) Test. It checks for “good isolation.”
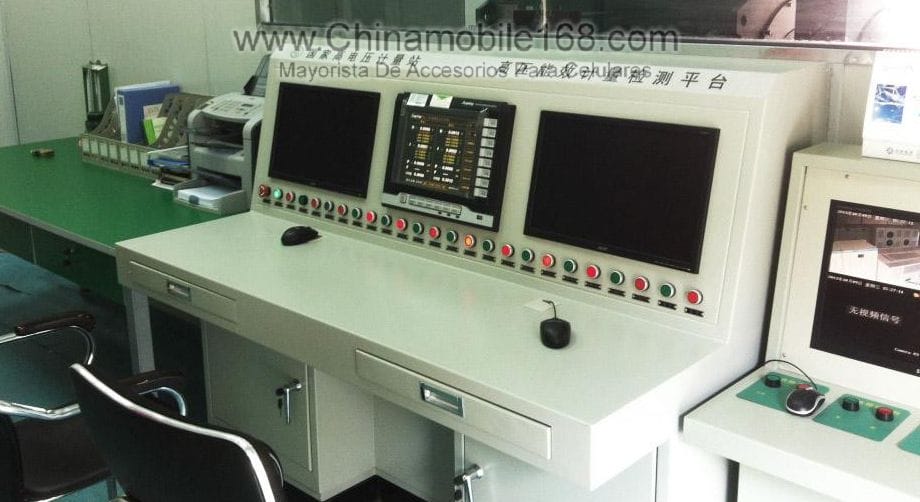
Ultrasound welding:
High-frequency ultrasonic acoustic vibrations are applied to plastic shells being held together under pressure to create a solid-state weld.
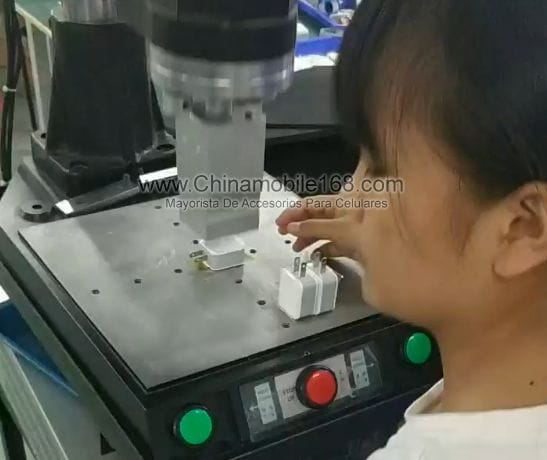
Burn in test
An electrical stress test that typically employs voltage and temperature to accelerate the appearance of latent reliability defects in a charger.
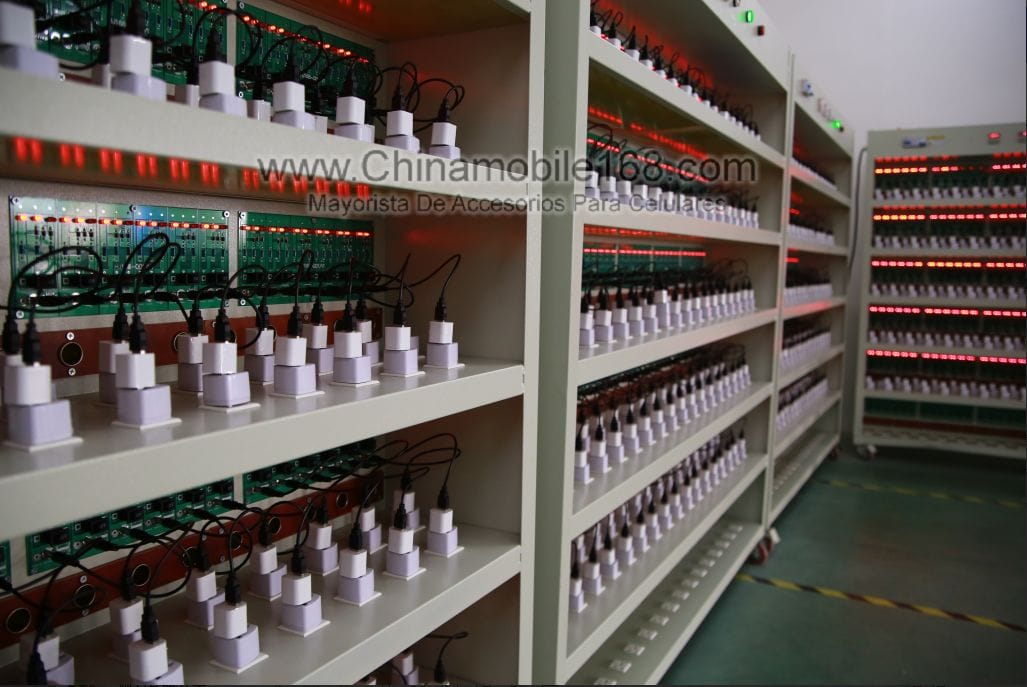
Listening inside noise
Swing the charger and listen to make sure that no components inside falling off.

Check Appearance
Check and make sure there are no defects on the surface.
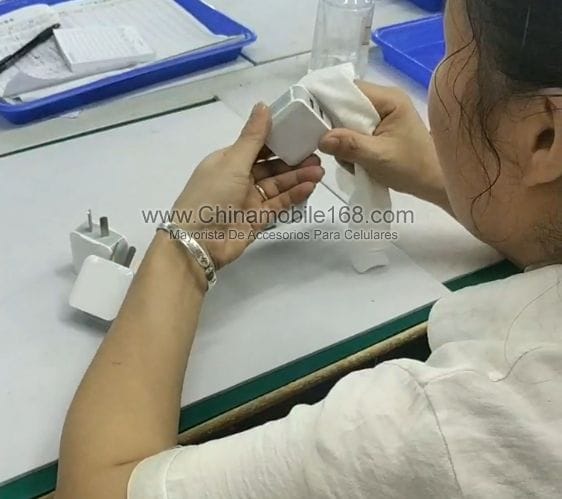
Packing and Put Into Warehouse
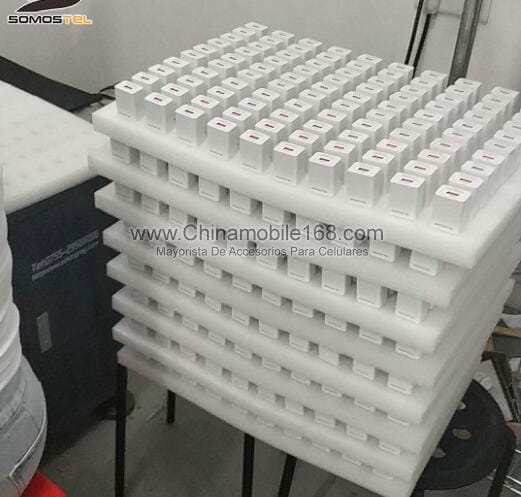
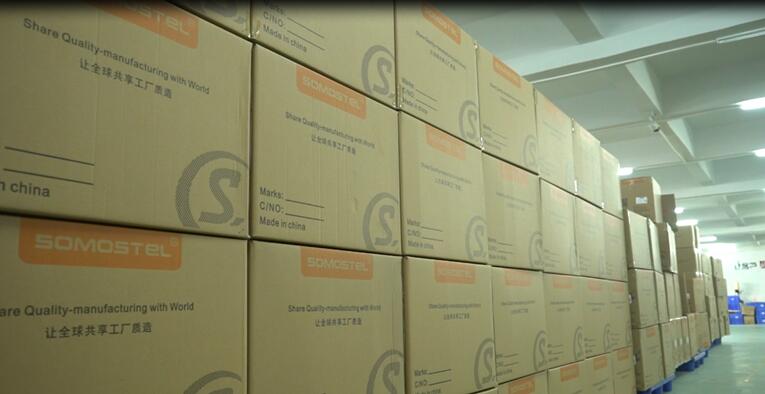